Les KPI production : définition, équation, exemples et TOP 3 des logiciels
Il est crucial d’analyser les performances de la chaîne de production pour pouvoir l’optimiser. Suivre les KPIs relève donc de l’indispensable car les données récoltées seront exploitées au service de la maximisation des performances des usines. En tant que directeur des opérations, piloter l’organisation et la productivité des usines marque un challenge et défi quotidiens.
Ce guide vous détaillera ce que sont les KPI de la production, leur importance, les principaux KPI à surveiller, et un comparatif des logiciels pour gérer votre production.
Production : définition et enjeux 🔗
Qu’est-ce que les KPI ?
Selon Asana, un indicateur de performance (ou KPI en anglais, pour key performance indicator) “est une mesure quantitative qui vous permet de suivre la progression de votre équipe ou organisation au regard de vos objectifs commerciaux clés“. Autrement dit, ces KPI représentent la donnée indispensable aux entreprises pour suivre les performances, mais aussi pour prendre des décisions qui impacteront l’organisation de celle-ci.
Pourquoi suivre les KPI production ?
Les KPI sont indispensables dans tous les services de l’entreprise que ce soit dans la vente, les achats, en marketing, en supply chain et donc aussi en production. En effet, ils fournissent des données objectives sur des aspects cruciaux comme par exemple le taux de rendement, la qualité des produits, l’efficacité des machines, et la productivité des équipes.
Finalement, sans ces mesures, il est difficile de savoir si les objectifs sont atteints ou si des ajustements sont nécessaires. Les KPI sont à la fois utiles pour identifier des problèmes, prendre des décisions éclairées, motiver les équipes mais aussi pour participer à l’amélioration continue.
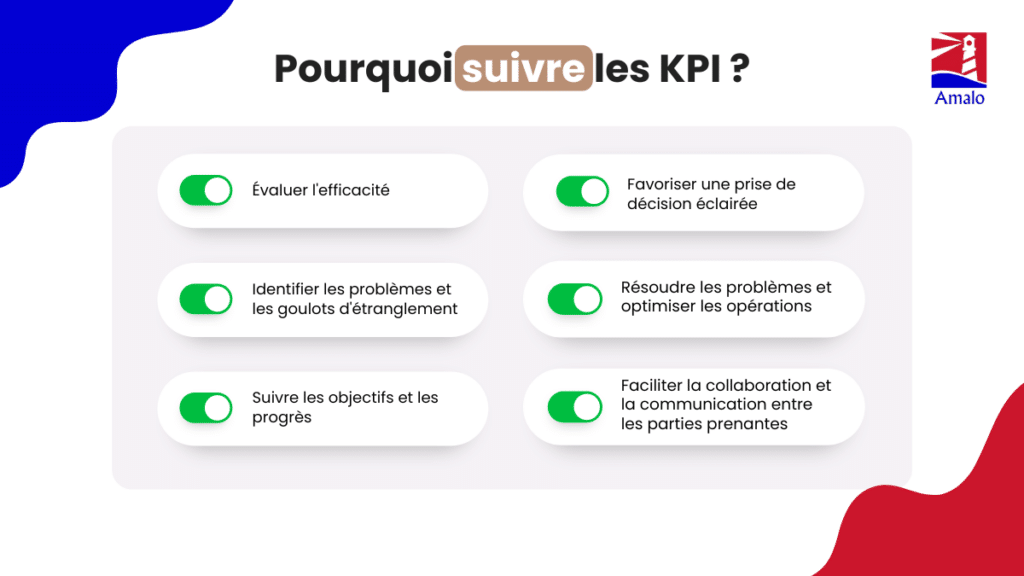
Les KPI à suivre pour maîtriser et optimiser la production 📊
Les KPI qui permettent de mesurer sa productivité
Taux de rendement global (TRG)
Le Taux de rendement global, aussi appelé OEE (Overall Equipment Effectiveness) est un indicateur qui permet de mesurer l’efficacité d’une machine ou d’un process. Finalement, il se calcule sur comme le rapport du temps utile sur le temps d’ouverture. Le temps utile constituant le temps passé à produire une pièce et le temps d’ouverture est le temps où l’usine fonctionne.
La formule du TRG est la suivante : TRG = Disponibilité × Performance × Qualité
Par ailleurs chaque composants de cette formule se calcule de la façon suivante :
- Disponibilité = Temps de fonctionnement / Temps prévu
- Performance = Production réelle / Production théorique
- Qualité = Produits conformes / Produits fabriqués
💡 Par exemple, si on prend un machine dans une usine de production qui fonctionne avec les conditions suivante :
- Temps prévu de fonctionnement : 8 heures (soit 480 minutes)
- Temps d’arrêt dû à la maintenance et aux pannes : 1 heure (soit 60 minutes)
- Production théorique : 100 pièces par heure (ce qui équivaut à 800 pièces en 8 heures)
- Production réelle : 700 pièces en 7 heures de fonctionnement effectif
- Produits conformes : 650 pièces (50 pièces étant défectueuses)
On peut calculer la disponibilité = 420 minutes (=7h de fonctionnement effectif) / 480 = 87,5 %
On calcule ensuite la performance = 700 / 700 = 100 %
Puis, on calcule la qualité = 650 / 700 = 92,9 %
Ainsi, le TRG = 87,5 × 100 × 92.9 = 81,3 %. On peut donc dire que la machine fonctionne à 81,3 % de son efficacité totale potentielle.
Les KPI clés pour analyser les capacités de son process
Durée moyenne d’un cycle de production
La durée moyenne du cycle de production correspond à la durée maximale de production. Si celle-ci est dépassée, cela peut engendrer des retards de production, une augmentation des coûts, une surchage des ressources ou encore impacter la satisfaction client. Ce KPI constitut une donnée importante à considérer puisque c’est celle-ci qui va donner la marche à suivre aux usines pour produire de façon efficace et rentable.
La formule de la durée moyenne d’un cycle de production est : DMCP = Somme des durées du cycle de production / nombre d’ordres planifiés
💡 Par exemple, si on suppose qu’une entreprise fabrique des widgets et qu’elle dispose de 3 machines différentes, voici les données pour la fabrication de 100 widgets.
- Machine A : 2h
- Machine B : 1,5h
- Machine C : 2,5h
- Le temps total pour traiter 100 widgets = 2 + 1,5 + 2,5 = 6 heures
Ainsi, la durée moyenne d’un cycle de production est = 6 / 100 = 0,06 heure/widget soit 3,6 minutes/widget. Finalement, il faut en moyenne 3,6 minutes pour qu’un widget soit produit
Pourcentage de la fluidité de la production
Ce pourcentage mesure l’efficacité de l’enchainement des processus de production, que ce soit sans interruption, ni retard. Il exprime le rapport entre le temps de production réellement fluide et le temps total de production planifié. Si ce pourcentage est élevé cela signifie que le flux de production est sans accroc et qu’il est optimal. Si celui-ci est faible, cela signifie que les processus sont inefficaces et qu’il y a des goulots d’étranglements.
La formule du pourcentage de la fluidité de la production est : %FP = (Volume de production réalisé dans les temps / total de la production de la période) x 100
💡 Par exemple, si on considère qu’une ligne de production peut produire 500 unités par jour, mais qu’en raison de plusieurs pannes ou encore arrêts non planifiés, elle ne parvient pas à produire assez. On gardera les données suivantes :
- Temps de production planifié : 8 heures (480 minutes)
- Temps d’arrêt total non planifié : 1h (60 minutes)
- Nombre d’unités produites : 400
- Nombre d’unités planifiées : 500
On calcule dans l’ordre :
- Temps de production effectif = 480 – 60 = 420 minutes
- Pourcentage de fluidité du temps = (420 / 480) x 100 = 87,5 %
- Pourcentage de fluidité de production = (400 × 500) x 100 = 80%
Finalement, 87,5 % du temps de production prévu a été utilisé efficacement sans interruptions mais on remarque parmi ce temps apartie, seulement 80 % des unités ont été effectivement produites.
Les KPI liés aux différents délais
Taux de respect des délais
Le taux de respect des délais (On Time Delivery) est une mesure qui permet de calculer le ratio de produits/pièces délivrés à temps par les usines par rapport au nombre total de produits/pièces finis.
Il existe deux équations pour calculer l’OTD = (nbr de commandes livrées dans les temps / nbr total de commandes livrées sur une période) x 100 ou (nbr de produits livrés/nbr de produits commandés) x 100
💡 Par exemple, on considère qu’une entreprise doit livrer 10 commandes au cours d’une semaine, on prend en compte les données suivantes
- Nbr total de commandes : 19
- Nbr de commandes livrées à temps : 8
- Nbr de commandes livrées en retard : 2
On calcule ainsi le taux de respect des délais = (8/10) x 100 = 80 %. Ainsi, 80 % des commandes on été livrées dans les délais prévus tandis que 20 % des commandes ont été livrées en retard.
Les KPI liés à la fiabilité des marchandises
Taux de défectuosité
Le taux de défectuosité est un indicateur qui mesure le pourcentage de produits défectueux par rapport au nombre total de produits fabriqués.
L’équation pour calculer le taux de défectuosité est : TD = (Nbr de produits défectueux / Nbr total de produits fabriqués) x 100
💡 Par exemple, on suppose qu’une entreprise fabrique 1000 unités par jour et qu’après le contrôle qualité, il s’avère que 50 unites sont jugées non-conformes donc défectueuses. On calcule le TD de la sorte = (50/100) x 100 = 5 %.
Ainsi, on peut conclure que 5 % des produits fabriqués au cours de la journée étaient défectueux. Plus le taux est élevé, plus cela signifie qu’il y a des problèmes dans le processus de fabrication ou dans le contrôle qualité.
Couverture des stocks critiques
La couverture des stocks critiques est un indicateur puissant qui permet de mesurer le nombre de jours (ou de périodes) pendant lesquels une usine peut continuer à produire et/ou vendre sans réapprovisionnement. Elle se calcule en se basant sur les stocks actuels de matières premières ou de produits finis.
Sa formule de calcule est la suite : CSC (en jours) = Stock actuel / Consommation quotidienne
💡 Par exemple, si on considère que la consommation quoidienne de la matière première d’une usine est de 50 unités et que le stock actuel de la MP est de 500 unités, on peut calcule la couverture de stocks critiques de cette façon.
CSC = 500 / 50 unités = 10 jours. Ainsi, cela signifie que l’usine peut continuer de produire pendant 10 jours sans réapprovisionnement de la matière première critique.
Les KPI liés à la fiabilité des équipements
Le pourcentage d’emploi des équipements
Le pourcentage d’emploi des équipements est une mesure qui indique l’utilisation des capacités de production d’une usine. Il mesure l’efficacité avec laquelle les équipements de production sont utilisés par rapport à leur capacité totale disponible.
Sa formule de calcul est la suivante : %EE = (Temps d’utilisation réel des équipements / Temps d’utilisation théorique max. des équipement) x 100
💡 Par exemple, si on considère qu’une usine dispose d’une machine peut fonctionner 8h par jour (480 minutes) mais celle-ci a été utilisée 6h (360 minutes). Ainsi on calcule (360/480) x 100 = 75 %.
La machine a donc été utilisée à 75 % de sa capacité totale disponible pendant la journée.
Les KPI liés aux ressources matérielles
Coût d’arrêt par équipement
Le coût d’arrêt par équipement se caractérise par la mesure de l’impact financier des arrêts non planifiés d’un équipement de production.
Son équation est la suivante : CAE = (Coût horaire de production) x Durée de l’arrêt.
💡 Par exemple, une usine utilise un machine critique dans son processus de production, on csondière les données suivantes :
- Durée de l’arrêt : 2 heures
- Coût horaire de production (perte de revenu) : 1000 € par heure
- Coût de réparation : 500 €
- Coûts supplémentaires (main-d’oeuvre, redémarrage, etc.) : 300 €
Ainsi on calcule dans un premier temps la perte de revenu avec la formule suivante : coûts horaire de production x durée de l’arrêt soit 1000 × 2 = 2000 €
Puis on calcule le coût total de l’arrêt = perte de revenu + coût de réparation + coûts supplémentaires soit 2000 + 500 + 300 = 2800 €. Ainsi, le coût d’arrêt par équipement est de 2800 € pour cet incident particulier autrement dit, l’impact financier de l’arrêt de la machine est de 2800 €.
Pourcentage taux de pertes
Le pourcentage de taux de pertes en production est un indicateur permettant de mesure la proportion de matières premières, produits semi-finis ou encore de produits finis qui sont perdus, gaspillés durant le processus de produits.
Pour le calculer, on utilise la formule suivante : %TP = (Quantité ou valeur des pertes de production / Quantité ou valeur produite) x 100
💡 Par exemple, si une usine utilise 10 000 kg de matière première pour produire un lot de chaises et que 500 kg de cette MP sont perdus ou gaspillés en raison de divers facteurs, on fera les calculs suivants = (500/10000) x 100 = 5 %.
Ainsi, le pourcentage de perte est de 5 %.
Pourcentage de fiabilité des plannings et des prévisions
Le pourcentage de fiabilité des plannings et des prévisions a pour objectif de mesurer la précision avec laquelle une usine respecte ses plannings et ses prévisions, tout simplement.
Sa formule de calcul esrt la suivante : %FPP = (Production réalisée / Production prévue) x 100
💡 Par exemple, si une entreprise produit 1000 unités d’un prduit au cours d’un mois et qu’à la fin du mois elle n’a produit que 950 unités, on calculera la fiabilité de la façon suivante : (950/1000) x 100 = 95 %
Ainsi, l’usine a réussi à produire 95 % de ce qui était prévu dans son planning de production.
Comment implémenter et suivre les KPI en production ?
Choisir les bons KPI
La première étape est de choisir les bons KPI à suivre et étudier. Afin de trouver les KPI qui seront les plus probants pour votre activité et votre volonté d’amélioration continue, ils doivent répondre à un certain nombre de critères :
- Alignement avec vos objectifs stratégiques
- La pertinence face à votre activité
- La mesurabilité qui doit être baséé sur des données précises et quantifiables
- L’actionnabilité et la fréquence de mesure qui vous permettra de réagir et prendre des décisions vite
- Qui regroupe l’ensemble de la chaîne de valeur reflètant ainsi toute la chaîne de production et pas que quelques aspects
- La conformité réglementaire en prenant en compte les exigences légales
- Et l’évolutivité afin qu’ils soient adaptables aux changements stratégiques
Choisir les bons outils et logiciels de suivi des KPI
Pour bien suivre les indicateurs de votre production, vous devez miser sur les bons outils. Il existe plusieurs outils de suivi de la production en France. Fini Excel et place à un logiciel qui apporte de la clarté en centralisant les données, qui permet l’automatisant et donc la précision en temps réel des données récoltées, qui vous permet de personnaliser vos KPi en fonction de vos besoins, qui rédige des rapports directement sur la plateforme et qui puisse s’intégrer à vos autres logiciels. Et surtout, le logiciel est un outil pour améliorer votre scalabilité.
En effet, un bon logiciel peut évoluer avec l’entreprise en s’adaptant aux changements que ce soit la taille de l’entreprise, l’augmentation du volume de production ou encore l’introduction de nouveaux processus. Et tout ça en garantissant une continuité dans le suivi des performances.
Bien analyser et interpréter les données
Suivre des KPI c’est bien, les analyser c’est mieux. Il est donc nécessaire de bien analyser ces données pour prendre des décisions éclairées. Ces décisions auront un impact direct sur la performance, la compétitivité ainsi que la pérennité de l’entreprise.
Dans un premier temps, l’analyse permet de réduire l’incertitudes en prenant des décisions sur des chiffres concrets plutôt que sur des suppositions ou intuitions. Le risque d’erreurs est considérablement réduit. Cette analyse permet également d’identifer les problèmes mais aussi les opprotunités de développement/réduction voir d’optimisation (des machines, des ressources, etc) de la chaîne de production. L’analyse participe également à l’amélioration conrinue.
Enfin, en analysant de façon précise et factuelle les données de la production cela permet d’améliorer la qualité des produits, améliorer la satisfaction client et par conséquent renforcer la compétitivité de l’entreprise.
TOP 3 des logiciels pour suivre la production
SAP S/4HANA, le logiciel de production par excellence
SAP S/4HANA est une suite ERP complète qui offre des solutions avancées pour la gestion de la production, des stocks, des prévisions, et des processus de fabrication. Il est particulièrement adapté aux grandes entreprises qui ont besoin de fonctionnalités robustes et intégrées.
🧢 Les avantages de SAP S/4HANA :
- Intégration totale avec d’autres modules SAP.
- Capacité de gestion en temps.
- Fonctionnalités avancées d’analyse.
Odoo, le logiciel de production français qui permet de gérer toutes les façettes de la chaîne de production et d’approvisionnement
Odoo offre une solution intégrée permettant aux entreprises de superviser leurs activités de chaîne de production et d’approvisionnement de manière modulaire et adaptable. Cette plateforme offre une vision globale, favorise la collaboration en temps réel et simplifie la gestion à tous les niveaux, contribuant ainsi à une efficacité opérationnelle accrue.
🧢 Les avantages d’Odoo :
- Plus de 370 fonctionnalités.
- Gain de productivité grâce à la centralisation.
- Interface modulable en fonction des besoins de l’entreprise.
SafetyCulture, le logiciel de production
SafetyCulture (anciennement iAuditor) est un logiciel qui optimise les processus de production en se concentrant sur la sécurité et la qualité grâce à des inspections numériques et un suivi des actions correctives. Il permet une prise de décision éclairée grâce à l’analyse des données collectées, tout en facilitant la collaboration en temps réel.
🧢 Les avantages de SafetyCulture :
- Intégration à d’autres solutions logicielles telles que ERP, CMMS et MES.
- Accessibilité sur le mobile pour suivre en temps réel.
- Conformité et sécurité renforcées.
Conclusion
En conclusion, une gestion efficace de la chaîne de production est essentielle pour maintenir la compétitivité et la performance d’une entreprise. L’évaluation et l’optimisation de cette chaîne complexe sont rendues possibles grâce à des indicateurs clés de performance (KPI) spécifiques à la production.
Ces KPI permettent de suivre et d’analyser des aspects critiques tels que le taux de respect des délais, le taux de défectuosité, l’emploi des équipements, la fluidité de la production, et le coût des arrêts. Le guide proposé offre une analyse détaillée des KPI de la production, expliquant leur importance, identifiant les principaux indicateurs à surveiller, et présentant un comparatif des logiciels de gestion de la production qui peuvent contribuer à une gestion optimisée.
Si vous souhaitez vous renseigner sur les KPI de la suply chain à suivre pour mieux optimiser la chaîne d’approvisionnement, nous avons rédigé un article complet.
FAQ : KPI production
Les erreurs fréquentes lors de la mise en place des KPi de la production sont :
– Choisir des KPI non pertinents
– Suivre trop de KPI qui entraîne une surcharge d’informations compliquant la prise de décision.
– Un manque de communication et d’engagement ainsi qu’une formation inadéquate des collaborateurs
– Une analyse des données trop pauvre
– Des objectifs irréalistes : il faut que les objectifs soient SMART
– Un non-ajustement des KPI en fonction de l’évolution de l’activité, suivi…
Il est important de se focaliser sur les KPI essentiels à savoir 5 à 10 KPI pas plus. Si vous concentrez trop de données, il sera difficile d’avoir une vision claire. 5 à 10 KPI bien choisis suffisent à fournir une vue d’ensemble claire et actionnable de la performance de la production. Ces KPI doivent couvrir les aspects critiques tels que la qualité, la productivité, les coûts, la sécurité, et les délais.
La fréquence d’analyse des KPI de la production dépend de plusieurs facteurs, tels que la nature de l’activité, la criticité des indicateurs, et les objectifs de l’entreprise. Cependant, certains KPI sont plus probants s’ils sont analysés de la façon suivante :
– Si vous souhaitez les analyser quotidiennement : Taux de rendement global (TRG), taux de défectuosité, temps d’arrêt des équipements, respect des plannings de production. Ces indicateurs nécessitent une surveillance continue pour réagir rapidement aux problèmes et assurer la fluidité des opérations quotidiennes.
– Si vous souhaitez les analyser hebdomadairement : Productivité des équipes, consommation des matières premières, taux de pertes, respect des délais de livraison. Ces indicateurs permettent d’identifier les tendances à court terme, d’ajuster les opérations, et de planifier les actions correctives nécessaires.
– Si vous souhaitez les analyser mensuellement : Coût de production, taux de fiabilité des plannings et prévisions, taux de couverture des stocks critiques, pourcentage de rendement des équipements. Ces indicateurs permettent d’évaluer la performance globale de la production, de détecter les écarts par rapport aux objectifs, et de prendre des décisions stratégiques pour les mois à venir.
– Si vous souhaitez les analyser trimestriellement ou annuellement ; Retour sur investissement (ROI) des initiatives d’amélioration, évolution de la qualité des produits, taux de satisfaction client lié à la production, efficacité énergétique. Ces analyses à plus long terme sont essentielles pour évaluer l’efficacité des stratégies mises en place, ajuster les objectifs à moyen ou long terme, et orienter les décisions de gestion de manière proactive.
Recruter des profils en production demande une compréhension fine des compétences techniques, des exigences opérationnelles, et des défis du secteur, ce qui rend le processus complexe et exigeant. En s’appuyant sur un cabinet de recrutement spécialisé en industrie, les entreprises minimisent les risques d’erreurs de recrutement et augmentent leurs chances de sélectionner les meilleurs talents, assurant ainsi la performance et la cohérence de leurs opérations industrielles. 🚀